Printers
About Flexo Printing
Flexographic printers are easy to install on any production line for a multitude of printing and coding needs. They range from small, economical printers for coding single items to wide format printers for printing messages on material several feet wide.
Pannier flexo printers and industrial printing inks can be used to print on nearly any flat material such as paper, plastic films, textiles, metals, and rubber. They are an excellent choice for these types of printing applications:
- Printed logos and messages are large
- The printed message does not change often
- Specific colors are required (e.g. Pantone colors)
- The budget for printing equipment is limited
- Simple/low-tech printing machines are desired
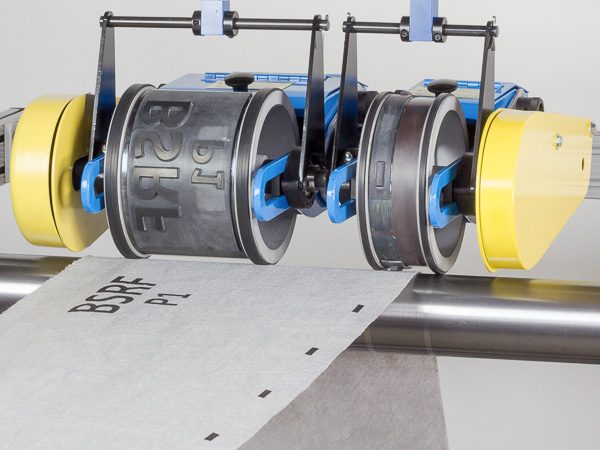
Friction Driven
Flexographic printers require no electric or air supply to operate. The wheels of the printer rotate in unison once the print wheel comes in contact with the material being printed. The friction created by the print wheel resting on the material causes it to turn. For more precise synchronization, an extended print wheel shaft can be tied directly to the line.
Continuous Inking
Once the wheels are in motion, the printer’s rolls will continuously pick up and apply a consistent film of ink to the printing plate. Solvents can be added to thin the ink and decrease drying time.
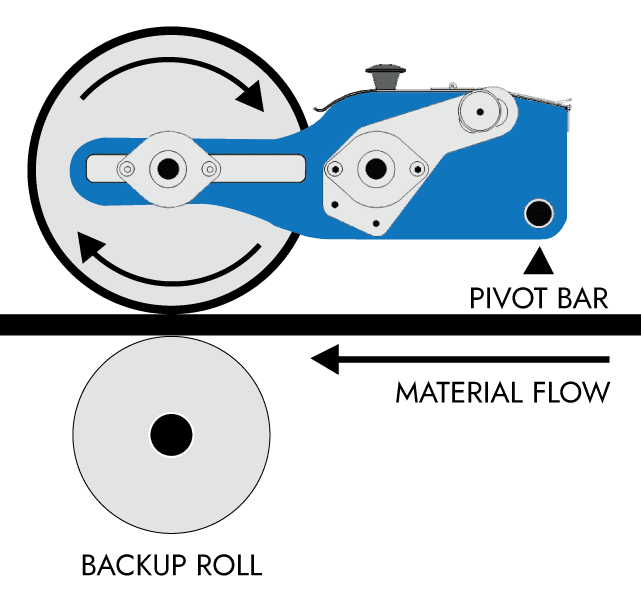
Flexo printers use either one or two rolls to pick up and apply ink to the print wheel which holds the printing plates or dies. The wheels are tied together with a chain and sprockets so that they turn in unison. The friction of the print wheel making contact with the moving material is what drives the rotation of all the printer’s wheels.
While there is little difference in print quality or ink usage with the two types of inking systems, there are some advantages to a single roll system:
- The doctor blade is the wear item compared to a pickup roll
- Fewer rolls means fewer adjustments to achieve proper contact pressure
- Fewer components to clean and replace
Printers are available in various sizes, from wide widths that can print material several feet wide to narrow widths that can be used alone or in groups. If several printers are used together, each one can be placed on or off line for runs of different size materials.
The most important consideration when purchasing a flexographic printer is the requirements of the printed message(s).
- How large is the overall size of message to be printed?
- How often must the message repeat on your material?
The answers to these questions will determine the width and circumference of the print wheel needed for your printing job.
Print Wheel Width
Your printing options are dictated by the width of the print cylinder. When choosing a wide printer, you will have the capability to print across a wide web or only a narrower width when needed, as shown below. Grouping narrow printers together also allows for flexibility in overall print width and message arrangement.
Print Wheel Circumference
The circumference of the print wheel determines:
- the maximum length of the printed message, and/or
- the maximum distance between the start of each print.
The Pannier Super Ink Print-All mini flexo printers feature a universal frame that can accommodate print wheels of different sizes. As shown in this image, the same size message can be printed with three different print wheels, but increasing the circumference of the wheel increases the space between each repeat of the message.